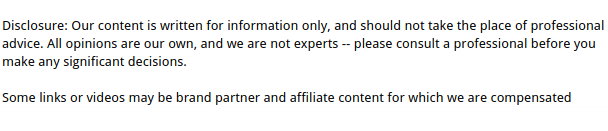
Most Americans are quite aware that computers are a fact of life, and that these machines can be found everywhere. Not only are desktop PCs and laptops good examples of computers, but also mobile phones, tablets, and even the components in cars all involve, or are, computers. Not everyone actually knows what goes inside those machines, but experts may be familiar with PCBs, or printed circuit boards. These PCBs are critical for any computer’s operation, and modern computing would not be possible without them. Computing has come a long way since the days of vacuum tubes and ENIAC. Now, computers boast ever-faster processing speeds and capabilities, and they need printed circuit boards to make that possible.
In fact, PCB manufacturing is so important and specialized, this PCB manufacturing is done separately from the overall manufacture of a computer. Dedicated factories and workshops are devoted to PCB manufacturing, and a PCB assembly service may make use of both human labor and robotic arms to create these delicate but important devices. What is there to know about PCB manufacturing and the demand for powerful, high quality PCBs?
How to Make a Printed Circuit Board
The exact work of engineering and building these printed circuit boards is a matter of advanced electronics, but the basic concept is quite clear. The engineers who design these boards make use of computer programs to create precise pathways of plastic and metal on these boards, and special software will lay out those patterns as needed. Electrical conducting paths tend to have very narrow spaces between them, often being just one millimeter apart, or even closer. What is more, these boards do not have to be limited to just one layer. Industry standards have called for boards with two, four, six, eight, or even 10 layers for improved processing power and capabilities. For some of the most demanding clients, a PCB manufacturing site may make a board with as many as 42 layers if need be.
When these printed circuit boards are being built, it is typically automated robotic arms and tools that will handle construction, having a great deal of precision in their work. When a work site involves a solder paste applier, a high-speed chip shooter, and even a pick-and-place machine and infrared oven. This allows a workshop to apply solder paste, and place and solder some 50,000 parts per hours, or even more. This allows for much faster work than if done by human hand, and setting up automated production lines allows some PCB assemblers to have a standard turn-in time of just five days (or even faster). This is 75% faster than the industry standard, in fact.
Care should be taken when assembling these printed circuit boards, however, since excessive heat will compromise them. Soldering quality is impacted by the temperatures involved, and until 160 degrees Celsius is reached, temperatures during manufacture should rise one or two degrees Celsius per second. However, if those temperatures rise too quickly, then this may melt delicate components and warp the circuit board, making it defective and even useless. Machines at the work site should be carefully programmed and inspected so that they use temperature correctly during work and don’t accidentally melt or warp the PCBs that they are making.
Other statistics have been gathered to monitor the efficiency of building these printed circuit boards. An Aberdeen Group survey has found, for example, that printed circuit boards represent around 31% of the cost of any product, meaning that those PCBs simply must be high quality so that the overall product’s quality does not suffer. What is more, around 53% of respondents to an Aberdeen Group survey said that their main PCB design issue to solve was to increase the complexity of their products. Many powerful computers today have a lot of work to do, and only complex and multi-layered PCBs can make that possible. Finally, the Aberdeen Group has also noted how often PCB manufacturing sites make prototypes for these products. On average, simple PCBs need 11.6 prototypes before mass production, but more complex ones with many layers may need as many as 16.1 prototypes, on average, before they are ready for mass production in earnest.